Case Study: Mouthpiece components used for COVID-19 patients
Client:
UK multi-disciplinary product design and product development consultancy (on behalf of a medical device client).
Challenge:
The challenge was to design and develop a novel cleaning and assembly process for plastic mouthpiece components used for COVID-19 patients.
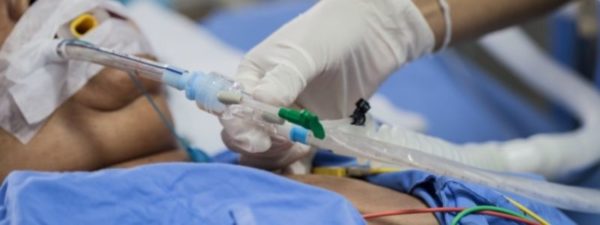
Design:
- Designed and developed an effective cleaning and drying system.
Build:
- Sourced suitable equipment and installed within a Class 7 cleanroom.
- Sourced suitable cleaning chemicals, and conducted COSHH/Risk Assessments.
- Provision of documentation for DHF, DMR and DHR and regulatory submissions.
- Production of devices for clinical use, including retail pouching, labelling, and final packaging.
Case Study: Assembly process for a complex single use retractor system
Client:
UK Spin Out Company focussed on cardiothoracic medical devices.
Challenge:
The challenge was to design and develop an assembly process for a complex single use retractor system.
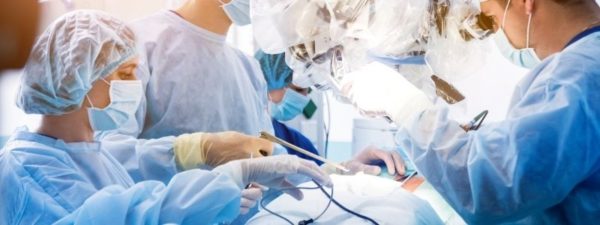
Design:
- Designed and developed a reliable, cost-effective and robust assembly process to produce the complex retractor device which met Client expectations.
Build:
- Developed and validated all processes and test methods, including blister tray sealing process.
- Designed and procured all primary and secondary packaging components.
- Provision of documentation for DHF, DMR and DHR and regulatory submissions.
- Production of devices for clinical use, including retail pouching, labelling, and final packaging.
Our experts develop bespoke medical devices and implantable textiles.